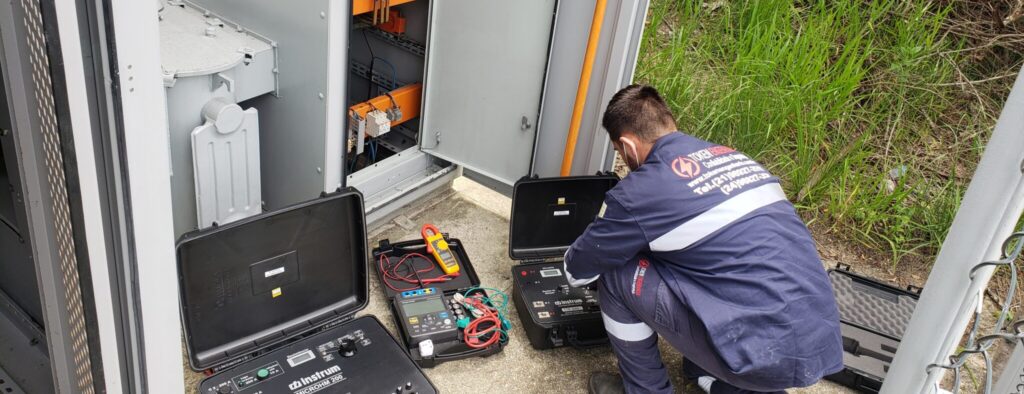
A manutenção de subestação de energia é uma atividade crucial para garantir a operação segura e confiável das instalações elétricas de alta tensão. Subestações são instalações que recebem, transformam e distribuem a energia elétrica de diferentes níveis de tensão, sendo uma parte essencial do sistema de transmissão e distribuição de energia. A manutenção adequada dessas subestações é importante para prevenir falhas, aumentar a vida útil dos equipamentos e garantir a segurança dos operadores e das instalações.
As atividades de Manutenção de Subestação de energia podem ser divididas em três categorias principais:
Manutenção preventiva: Essa é uma manutenção programada e planejada realizada regularmente para evitar problemas futuros. Inclui a inspeção visual dos equipamentos, limpeza, aperto de conexões, medição de parâmetros elétricos, análise de óleo isolante (caso a subestação tenha transformadores) e outros testes de rotina para identificar possíveis desgastes ou falhas em estágios iniciais.
Manutenção corretiva: Essa manutenção é realizada após a ocorrência de falhas ou problemas em algum componente da subestação. É importante solucionar essas falhas o mais rápido possível para evitar interrupções no fornecimento de energia ou danos mais graves aos equipamentos.
Manutenção preditiva: Essa é uma abordagem mais avançada que utiliza técnicas de monitoramento contínuo para prever falhas em componentes específicos antes que elas ocorram. Isso envolve o uso de tecnologias como termografia infravermelha, análise de vibração, monitoramento de descargas parciais, entre outras.
As atividades específicas de manutenção dependerão do tipo de subestação, de sua capacidade, dos equipamentos presentes (como transformadores, disjuntores, chaves seccionadoras, etc.) e das normas técnicas aplicáveis.
É fundamental que a manutenção de subestação seja realizada por profissionais qualificados e experientes, pois o trabalho envolve altas tensões e riscos significativos. Além disso, a manutenção deve estar em conformidade com as regulamentações de segurança elétrica e com as recomendações dos fabricantes dos equipamentos. Uma manutenção adequada garante a confiabilidade operacional da subestação, minimiza o risco de falhas catastróficas e contribui para o fornecimento seguro e contínuo de energia elétrica.
Quais São os Principais Ensaios e Testes Executados na Manutenção de Subestação?
Na manutenção de subestações, são realizados diversos ensaios e testes para verificar o estado e o desempenho dos equipamentos elétricos presentes. Esses ensaios têm o objetivo de identificar possíveis falhas, desgastes ou problemas que possam comprometer a segurança e a eficiência das instalações. A seguir, estão alguns dos ensaios mais comuns executados na manutenção de subestações:
Ensaio de Resistência de Isolamento: Esse ensaio mede a resistência de isolamento entre os condutores e aterramentos, verificando se não há correntes de fuga que possam causar falhas elétricas.
Ensaio de Resistência Ôhmica de Contatos: É realizado para verificar a resistência elétrica de contatos, como nos disjuntores, chaves seccionadoras e outros dispositivos de manobra.
Ensaio de Fator de Potência (Dissipação Dielétrica): Esse ensaio avalia a qualidade do isolamento dos equipamentos e transformadores, analisando a dissipação dielétrica.
Medição de Tensões e Correntes: São realizadas medições das tensões e correntes em diferentes pontos da subestação para verificar se estão dentro dos parâmetros esperados.
Termografia Infravermelha: Esse ensaio utiliza uma câmera termográfica para identificar pontos de aquecimento anormais, que podem indicar problemas de conexão ou desgastes em equipamentos.
Medição de Resistência de Aterramento: É feita a medição da resistência do sistema de aterramento para garantir a eficiência e a segurança do mesmo.
Ensaio de Proteção e Relés: Teste dos sistemas de proteção e relés para verificar se estão operando corretamente e protegendo a subestação de eventos indesejados.
Ensaio de Disparo e Fechamento de Disjuntores: Verificação do funcionamento correto dos disjuntores em situações de abertura e fechamento.
Análise de Óleo Isolante (caso haja transformadores): Realização de ensaios físico-químicos no óleo isolante dos transformadores para avaliar o seu estado.
Esses ensaios são realizados por profissionais qualificados e seguem as normas técnicas e regulamentos aplicáveis. Os resultados desses ensaios são utilizados para identificar eventuais problemas e definir ações corretivas e preventivas a serem tomadas para garantir a confiabilidade e segurança das instalações elétricas da subestação. A manutenção de subestação de energia regular e adequada é essencial para o bom funcionamento da subestação e para a prevenção de falhas e acidentes.
O que é um teste de Resistência de Isolamento e Por Que é Importante?
O teste de resistência de isolamento, também conhecido como teste de Megger, é uma forma de medir a eficácia do isolamento em equipamentos elétricos como transformadores, motores, cabos, interruptores, etc. O teste é realizado aplicando uma tensão específica ao equipamento e medindo a quantidade de corrente que pode fluir através do isolamento. A resistência é então calculada usando a lei de Ohm (V=IR), onde V é a tensão aplicada e I é a corrente medida.
O objetivo do teste de resistência de isolamento é garantir que o isolamento do equipamento elétrico seja suficientemente forte para resistir à tensão elétrica. Isolamentos que não possuem uma resistência adequada podem permitir uma quantidade excessiva de corrente elétrica passar por eles, o que pode resultar em falhas de equipamentos, curtos-circuitos e possíveis riscos à segurança, como incêndios ou choques elétricos.
Portanto, o teste de resistência de isolamento é importante por várias razões:
Prevenção de falhas: Ao realizar este teste, problemas com o isolamento podem ser detectados antecipadamente, antes que causem falhas nos equipamentos, minimizando o tempo de inatividade e os custos de reparo.
Garantir a segurança: O teste ajuda a garantir que o equipamento elétrico seja seguro para operar, minimizando o risco de choques elétricos ou incêndios.
Conformidade com normas: Em muitos casos, testes regulares de resistência de isolamento são exigidos por normas de segurança elétrica ou seguradoras.
Manutenção Preditiva: O teste de resistência de isolamento é uma parte importante da manutenção preditiva, ajudando a identificar problemas potenciais antes que se tornem sérios. Ao comparar leituras ao longo do tempo, as tendências na degradação do isolamento podem ser identificadas.
O que é um Teste de Relação de Transformação (TTR) e Por Que é Importante?
O TTR é realizado aplicando-se uma tensão conhecida ao enrolamento primário do transformador e medindo a tensão que resulta no enrolamento secundário. A razão das duas tensões deve ser igual à razão de transformação especificada pelo fabricante.
Este teste é importante por várias razões:
Verificação das especificações: O teste de TTR garante que o transformador foi fabricado de acordo com as especificações e que a relação de voltas é a correta. Isso é especialmente importante quando o transformador é fabricado.
Identificação de problemas de fabricação ou montagem: Problemas com a relação de voltas do transformador podem indicar problemas de fabricação ou montagem, como enrolamentos incorretamente conectados ou enrolamentos com voltas ausentes.
Detecção de problemas operacionais: Alterações na relação de transformação durante a vida útil do transformador podem indicar problemas como curto-circuito entre voltas, que pode eventualmente levar à falha do transformador.
Garantia da operação correta: A relação de transformação correta é essencial para a operação correta do transformador e do sistema elétrico como um todo. Uma relação de transformação incorreta pode levar a condições de tensão ou corrente inadequadas, o que pode danificar o equipamento e criar riscos de segurança.
Portanto, o teste de TTR é uma parte essencial da manutenção do transformador e deve ser realizado regularmente, bem como sempre que um transformador for reparado ou instalado.
Leia mais sobre o Assunto em nosso Artigo:
O que é um Teste de Resistência Ôhmica e Por Que é Importante?
O teste de resistência ôhmica, também conhecido como teste de resistência de enrolamento, é um procedimento realizado em transformadores, motores e outros equipamentos elétricos para medir a resistência dos seus enrolamentos. Ele é realizado aplicando uma pequena corrente contínua (CC) através do enrolamento e medindo a queda de tensão resultante. A resistência é então calculada usando a lei de Ohm (V = IR).
Esse teste é extremamente importante por várias razões:
Verificação de especificações do fabricante: Esse teste ajuda a verificar se os enrolamentos do equipamento elétrico estão de acordo com as especificações do fabricante. Uma resistência fora do esperado pode indicar um problema com o enrolamento, como uma espira em curto ou uma conexão inadequada.
Detecção de problemas: A resistência dos enrolamentos pode mudar ao longo do tempo devido à degradação dos materiais, conexões soltas, ou danos físicos. Ao realizar um teste de resistência ôhmica regularmente, esses problemas podem ser detectados cedo e corrigidos antes que levem a falhas mais graves do equipamento.
Balanceamento de fase: Em equipamentos trifásicos, a resistência dos enrolamentos de cada fase deve ser igual. Se houver um desequilíbrio significativo, isso pode indicar um problema que precisa ser corrigido.
Avaliação da qualidade do reparo: Após a manutenção ou reparo de um equipamento, o teste de resistência ôhmica pode ser usado para confirmar que os enrolamentos foram corretamente reconectados e que o equipamento está em condições adequadas para ser colocado de volta em operação.
Em suma, o teste de resistência ôhmica é uma ferramenta valiosa para garantir a operação adequada do equipamento elétrico e prevenir falhas do sistema.
O Que é uma Análise de Óleo de Transformador e por que é Importante?
A análise de óleo de transformador é um procedimento que avalia a condição do óleo isolante usado em um transformador. O óleo de transformador desempenha dois papéis críticos: ele atua como um meio isolante, prevenindo descargas elétricas entre as diferentes partes do transformador, e também ajuda a dissipar o calor gerado durante a operação do transformador, mantendo-o resfriado.
A análise de óleo de transformador pode envolver vários testes diferentes, incluindo:
Teste de rigidez dielétrica: Mede a tensão máxima que o óleo pode suportar antes de se romper e permitir um arco elétrico.
Teste de conteúdo de umidade: Mede a quantidade de água presente no óleo. A umidade pode reduzir a eficácia do óleo como isolante e também pode levar à formação de ácidos prejudiciais.
Teste de conteúdo de gases dissolvidos (DGA): Mede a quantidade e os tipos de gases presentes no óleo. Certos gases podem ser produzidos por problemas específicos no transformador, como arcos elétricos, superaquecimento ou descargas parciais.
Teste de conteúdo de partículas: Mede a quantidade de partículas sólidas presentes no óleo. Partículas podem ser um sinal de desgaste mecânico ou deterioração do isolamento de papel.
Teste de acidez: Mede a acidez do óleo, que pode indicar a presença de compostos corrosivos.
Teste de Fator de Potência ou Tangente Delta: Este teste mede as perdas dielétricas no óleo, o que pode indicar problemas com a qualidade do óleo.
Esses testes são importantes porque a condição do óleo do transformador pode ter um grande impacto no desempenho e na vida útil do transformador. Se o óleo estiver contaminado ou se suas propriedades estiverem fora das especificações, isso pode reduzir a eficácia do óleo como isolante e refrigerante, potencialmente levando a falhas no transformador. A análise de óleo de transformador também pode ajudar a identificar problemas emergentes no transformador antes que se tornem graves, permitindo que as ações corretivas sejam tomadas em tempo hábil. Portanto, a análise de óleo de transformador é uma parte essencial da manutenção preventiva do transformador.
Por que os Disjuntores são testados e Quais tipos de testes são Realizados?
Os disjuntores desempenham um papel fundamental na proteção dos sistemas elétricos. Eles são projetados para interromper o fluxo de corrente elétrica em caso de sobrecarga ou curto-circuito, prevenindo danos ao equipamento e garantindo a segurança dos operadores. Devido à sua importância, é essencial garantir que os disjuntores estejam funcionando corretamente, e é por isso que são submetidos a testes regulares.
Aqui estão alguns dos principais testes realizados em disjuntores:
Teste de Tempo de Operação: Este teste verifica se o disjuntor está operando dentro do tempo especificado pelo fabricante. A velocidade de operação é crítica para a proteção do sistema.
Teste de Resistência de Contato: Este teste mede a resistência nos contatos do disjuntor. Uma alta resistência pode indicar problemas como contatos queimados ou corroídos, que podem afetar a operação do disjuntor.
Teste de Resistência de Isolamento: Este teste verifica a resistência do disjuntor à passagem de corrente através de suas partes isolantes. Uma baixa resistência de isolamento pode indicar um problema, como umidade ou sujeira, que pode levar a um mau funcionamento do disjuntor.
Teste de Rigidez Dielétrica: Este teste aplica uma alta tensão ao disjuntor para garantir que ele possa suportar tensões elevadas sem quebrar o isolamento.
Teste de Corrente de Fuga: Este teste verifica a corrente que escapa do circuito quando o disjuntor está fechado, o que pode indicar problemas de isolamento.
Teste de Funcionamento Mecânico: Este teste verifica a operação mecânica do disjuntor, incluindo o mecanismo de operação e os dispositivos auxiliares.
Realizar esses testes é importante para garantir que os disjuntores estão funcionando corretamente e são capazes de proteger o sistema elétrico conforme esperado. Testes regulares também podem ajudar a identificar problemas potenciais antes que causem falhas de equipamentos, interrupções de serviço ou outros problemas.
Por que é Importante Testar os Relés de Proteção e como eles são Testados?
Os relés de proteção são componentes críticos nas subestações e em outros sistemas elétricos. Eles monitoram as condições do sistema e, se detectarem uma condição anormal (como uma sobrecarga ou um curto-circuito), enviam um sinal para interromper o fluxo de corrente, protegendo assim o equipamento de danos.
Testar os relés de proteção é fundamental por várias razões:
Verificação do Funcionamento Correto: Os relés de proteção são essenciais para a operação segura de um sistema elétrico. Se falharem em operar corretamente durante uma condição de falha, o resultado pode ser danos ao equipamento, interrupção do fornecimento de energia, ou até mesmo riscos à segurança.
Verificação das Configurações de Relé: Os relés de proteção geralmente precisam ser configurados para o sistema específico em que estão instalados. Os testes podem ser usados para verificar se as configurações do relé são adequadas.
Detecção de Problemas Potenciais: Testes regulares podem ajudar a identificar problemas emergentes antes que causem uma falha no relé ou no sistema.
Existem várias maneiras de testar os relés de proteção. Algumas delas incluem:
Testes de Injeção de Corrente e Tensão: Nesses testes, são injetadas correntes e/ou tensões conhecidas no relé, e o seu comportamento é observado para verificar se está operando conforme esperado.
Testes Funcionais: Nesses testes, são simuladas condições de falha específicas para verificar se o relé responde adequadamente.
Testes de Tempo de Operação: Nesses testes, é verificado se o relé opera dentro do tempo esperado quando uma condição de falha é simulada.
Verificação de Configurações: As configurações do relé são verificadas para garantir que estejam corretas para o sistema em que o relé está instalado.
Ao realizar esses testes regularmente, é possível garantir que os relés de proteção estejam funcionando corretamente e protegendo o sistema elétrico conforme esperado.
O que é a Inspeção Termográfica na Subestação de Energia e por que é Importante?
A inspeção termográfica em uma subestação de energia é um processo que utiliza câmeras de infravermelho para criar uma imagem térmica (termograma) dos componentes da subestação, incluindo transformadores, disjuntores, chaves seccionadoras, conexões e outros equipamentos. Essas imagens permitem que os técnicos vejam a distribuição de calor nos componentes, o que pode ajudar a identificar problemas antes que causem falhas.
Aqui estão algumas razões pelas quais a inspeção termográfica é importante em uma subestação de energia:
Detecção de Pontos Quentes: Componentes elétricos, como disjuntores, conexões, transformadores e cabos, tendem a aquecer antes de falhar. A inspeção termográfica pode identificar esses “pontos quentes” antes que uma falha ocorra, permitindo que a manutenção seja realizada de forma preventiva.
Inspeção Não Invasiva: A inspeção termográfica é uma técnica de inspeção não invasiva, o que significa que não requer contato físico ou interrupção do equipamento. Isso a torna segura e conveniente para inspecionar equipamentos elétricos em operação.
Inspeção Rápida de Grandes Áreas: Câmeras de infravermelho podem rapidamente varrer grandes áreas ou vários componentes, tornando a inspeção termográfica uma maneira eficiente de realizar inspeções regulares de subestações e outros sistemas elétricos.
Detecção Precoce de Problemas: Além de pontos quentes, a inspeção termográfica também pode detectar outras anomalias térmicas que podem indicar problemas, como umidade em isoladores ou refrigeração inadequada em transformadores.
A inspeção termográfica, portanto, é uma ferramenta poderosa para manter subestações e outros sistemas elétricos funcionando de maneira segura e eficiente, prevenindo falhas e reduzindo o tempo de inatividade.
Leia mais sobre o Assunto em Nossos Artigos e Páginas de Referências:
- Termografia Elétrica;
- Inspeção Termográfica em Painel elétrico;
- O que é Inspeção Termográfica e Para que Serve?;
- O Que é Laudo Termografia e Qual a Sua Aplicação?;
- O que é Termografia Infravermelho e como é Usada?.
Qual é o Objetivo da Manutenção e Teste das Baterias em Uma Subestação de Energia?
As baterias em uma subestação desempenham um papel crucial, pois fornecem a energia de reserva para manter a operação dos sistemas de controle, proteção e comunicação no caso de uma falha de energia ou interrupção do fornecimento principal de energia. Isso pode ser especialmente crítico durante uma falha de energia, quando as proteções e controles da subestação devem continuar funcionando para garantir a segurança e possibilitar a restauração da energia.
Dada a importância das baterias, a manutenção e os testes regulares são essenciais para garantir que elas estarão prontas para operar quando necessárias. A manutenção e os testes de baterias em uma subestação geralmente têm os seguintes objetivos:
Verificar a Condição da Bateria: A manutenção regular pode incluir inspeções visuais para verificar a condição física da bateria, como a presença de corrosão, vazamentos ou danos.
Testar a Capacidade da Bateria: Testes de capacidade, também conhecidos como testes de carga, são realizados para verificar se a bateria pode fornecer a quantidade esperada de energia. Isso geralmente é feito descarregando a bateria e medindo a quantidade de energia que ela pode fornecer.
Verificar a Tensão e a Corrente da Bateria: A tensão e a corrente da bateria são verificadas regularmente para garantir que estão dentro das especificações. Variações na tensão ou corrente podem indicar problemas, como uma célula defeituosa.
Verificar e Manter os Níveis de Eletrólito: Para baterias que usam um eletrólito, como as baterias de chumbo-ácido, os níveis de eletrólito são verificados e mantidos para garantir o funcionamento adequado.
Testar os Sistemas de Carregamento da Bateria: Os sistemas de carregamento da bateria também são testados para garantir que estão funcionando corretamente e que a bateria será carregada adequadamente após ser descarregada.
Manter e testar regularmente as baterias de uma subestação é um passo essencial para garantir a confiabilidade e a segurança da subestação e do sistema elétrico como um todo.
Leia mais sobre Subestação de Energia em nossas páginas de referências:
- Manutenção de Subestação de Energia;
- Projeto de Subestação de Energia;
- Montagem de Subestação de Energia;
- A Importância da Manutenção de Subestação de Energia.
Entre em contato conosco para receber uma proposta.